The first step when it comes time to designing your own prefab home is to consider where you’d like it to go. While there’s plenty of flexibility with modular designs, there can be limitations with your site, such as access. For example, when Modscape delivers its builds, trucks are used for transportation and cranes used for installation.
“It’s important to assess whether a truck can get there safely. If you’re unsure, you can always contact us and we’ll figure it out for you,” says Modscape’s Boon Mark Souphanh.
Based in Melbourne, Modscape has been harnessing the power of modular construction since 2006. With more than 500 projects completed to date, modular construction is suitable for residential, commercial and hospitality applications.
“We’re essentially a one-stop-shop that makes the process of designing and building a new home enjoyable and hassle-free. Rarely do you see a modular builder with its own team of talented architects, designers and project delivery staff.”
Concept design
While it’s one thing to admire modular and prefab projects from a distance, it’s a whole new experience in person.
“Typically, most clients come in for a site tour of our facility and display suite before our in-house design team carries out a site inspection. This enables our architects to assess access, passive orientation and siting options, which will inform a concept design,” explains Boon.
From here, the architects take the proposal and work collaboratively with the client to develop and refine the building’s design. And the possibilities are endless: “Modscape designs bespoke modular homes – we’re not ‘cookie-cutter’ in the sense that we don’t work off set plans or design templates. Your home will be unique.”
Construction
Each modular building brought to life at Modscape’s construction hub uses the building methodology of ‘Design for Manufacture and Assembly’ (DfMA) to ensure the most efficient process possible.
“DfMA focuses on the ‘kit of parts’ that make up the whole project – minimising and streamlining these parts to enhance the speed, quality and sustainability of the final product. We effectively optimise the systems and details across the installation stages to make this process simpler and more efficient,” says Boon.
From design to the completion of your modular home, the entire process with Modscape takes 12 weeks, and then it is time for delivery.
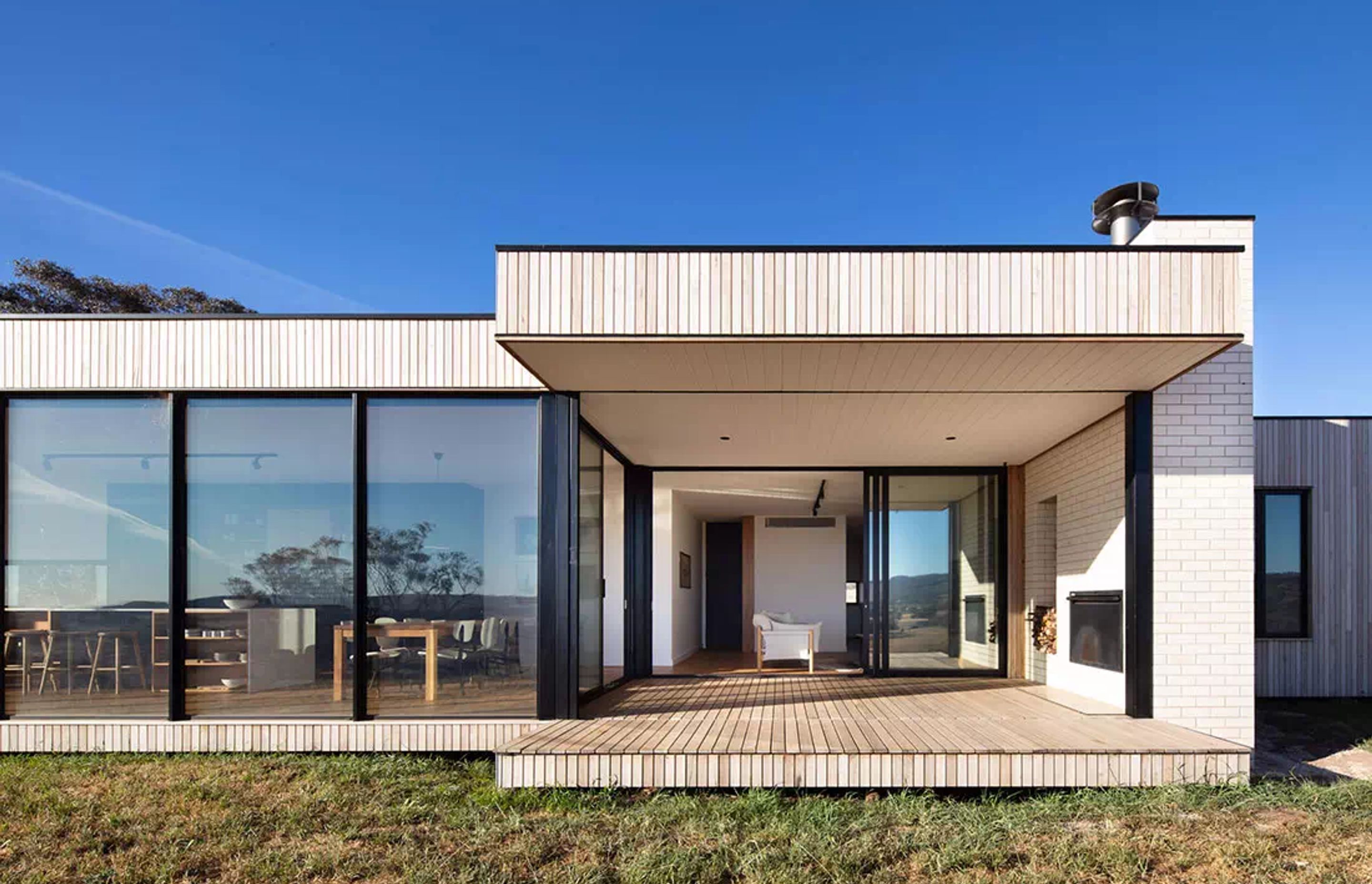
Site preparation and delivery
As well as ticking all of the boxes with permits and documentation, utilities such as water, power and sewerage need to be ready before installation. Once this has been completed, the new home is delivered to the site.
The modules are loaded onto trucks and delivered to the site, Boon says, adding that in some circumstances, the trucks may be able to reverse in between the footings to lower modules down into position. Most projects require a crane, however.
Either way, the installation of the modules generally takes only one day.
To learn more, explore Modscape’s work on ArchiPro.