QBS Construction isn't just renovating a two-storeyed 1920s bungalow in Parnell, it has adopted a new method of moving the house on site to save time and money and reduce risk of injury.
Currently, under construction in Parnell, a simple 1920s two-storeyed timber bungalow is undergoing a transformation. As one of the earlier homes in the surrounding area, QBS Construction director and project manager Troy Jury believes the house was once the home of the reverend of Holy Trinity Cathedral in Parnell and, potentially, could have been on same plot of land as the cathedral. It includes a number of crafted features, including original mouldings and ceilings, rimu timber floors, and a stunning stained-glass window scene of Rangitoto Island.
For the past ten years, the house has been owned and lived in by a professional couple, who both work nearby, love the home and want to stay in the area for the long-term. They decided to modernise the home to make it a more practical family home for the future, with parking onsite as there was previously none, as well as more room for their growing family. The most sensible solution was to raise the house and build a 220m m2 basement underneath to include a three-car garage, a new media room, and a lift shaft to make it easy to transfer groceries up into the kitchen.
“Traditionally, when building a basement under an existing home, people have propped the house up and dug underneath. But, this can be a really dangerous and it’s an extremely slow process that has an effect on the labour force; people have actually been killed in New Zealand using this method,” explains Troy.
In recent years, QBS has adopted a process that comes from Sweden and uses a hydraulic lifting system. It was first used in New Zealand after the Canterbury earthquakes, when a company called House Lifters NZ started working with the system to move quake-damaged houses out of the way while the foundations were being rebuilt.
“Most people think it’s too expensive to move an existing home but, actually, it’s far safer to move the house out of the way of the building works, and it also means that we’ve been able to work through the winter – even, in the mud and rain. However, a propped-up house risks sinking or collapsing in adverse weather. We were able to do it in half the time by moving the house away,” he says. The house was slid off its foundations and moved 28 metres to the back of the section onto temporary foundations. It is a steep section on a 30-degree rake and, at the highest point, the house is suspended 12 metres up in the air. “To slide the house, it was set up on two large steel beams with about 30 rolls on them – each about the size of shoe box and weighing 8kg,” says Troy. “The steel goes in under the existing house and out onto the temporary foundation; then, we used a standard manual winch and two guys slowly moved the house at a rate of 100mm per minute, which is actually pretty quick, and it took about 4–1/2 hours to move the house 28 metres.”
From start to finish, the entire moving process – from its existing to temporary foundations, building the basement and returning the house back to its permanent location – took about 3–1/2 months.“ By comparison, if we were to prop the house up on acrow props and work underneath, it would have taken 9–12 months to build the basement, and the cost of having guys on site for that long would have been huge.”
To prepare the old house for the move, an engineer was required to work out some of the crucial calculations, such as how deep the temporary foundations needed to be and how many braces were required to support the house. “We removed the exterior foundations and worked with the existing structural loading points on the house to support those areas,” says Troy. “That’s very important because, if the supports were put in the wrong places, then the house could sag.”
To prepare the back yard as a temporary site for the house, geotechnical testing of the soil was performed to ascertain at what depth the poles needed to be installed in order to support 75 tonnes of house. The QBS team then built temporary foundations out of 300mm-wide SED timber piles up to 15m tall, which were sunk 3m into the soil and rising up to 12m out of the ground.
The temporary foundations were designed to hold the house for a best-case scenario of three months to a worst-case scenario of 12 months, rather than the 50-plus years required of permanent foundations. “The worst-case scenario is that the house slips down the hills, so we needed to mitigate against that happening,” says Troy.
It was fortunate that the existing timber subfloor of the house was structurally sound, so all that was required to support the timber structure was temporary bracing on the walls to stop the house from raking, which is when it can twist out of shape. “Of course, as a result of the move, you end up with some surface cracks on the walls and so on, but since the house was being renovated, that wasn’t an issue,” explains Troy.
To move a house in this way, Troy says it doesn’t matter how the land lies, just that there is space on the property to temporarily re-site the house. But, it there isn’t space onsite but the street is wide enough and the access is sufficient, then, depending on the size of the house, it can be moved temporarily to a yard, while the basement is under construction.
The process of moving the house has been successful,” says Troy. “We’re lucky that this site is a perfect situation, with plenty of room to move the house into the back yard – and while it’s not a really easy process to do, it gives people lots of options.” The team is currently into the next stage of renovating and restoring the house, which involves tying it back into the existing foundations, lowering the house onto its new block base, cutting through the floors and adding in the lift shaft, and cladding the block in concrete, timber and weatherboard so it will look like the existing house.
Then, the final stage involves backfilling the section to make it level, landscaping – including outdoor living spaces and covered decks, and new traditional fencing. The completed house will also host four bedrooms and an office, an open-plan living, dining and kitchen area, and is due for completion later in 2020.
Words by Justine Harvey.
Renders by Bespoke.
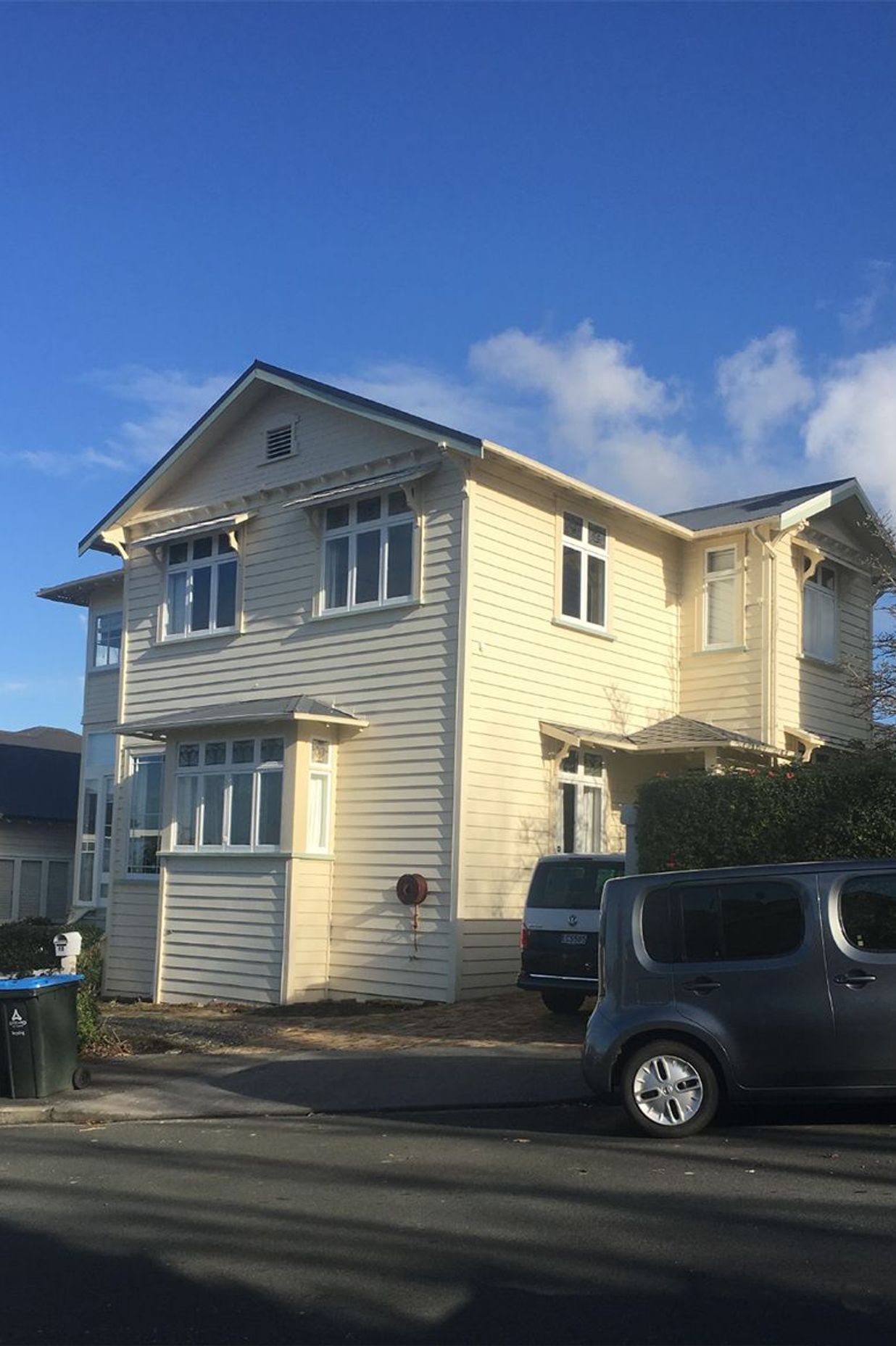