More people are aware of modular construction and its benefits than ever before, and huge market growth is forecasted for years to come. That said, there are still some common misconceptions about this innovative building methodology that need some serious debunking. Modular construction itself has evolved dramatically in the past decade. Many of the initial perceived ‘shortcomings’ are now things of the past, and new innovations are being realised every day.
Here are four of the most common modular/prefabricated construction myths, and why you shouldn’t make the mistake of buying into them:
- A modular home is just a fancy name for a mobile home
Mobile homes were phased out of production way back in 1976, but many still incorrectly associate them with modular homes.
Modular homes and mobile homes are both built-in factories, but that’s where the similarities end for the most part. Built to a much higher standard, modular homes must follow local building codes in the state they’re installed. Additionally, they are often manufactured in multiple pieces – or ‘modules’ – whereas mobile and manufactured homes are a single piece.
There is no standard size module, as they are customised to suit each design. Each modular project is essentially a sum of parts as the maximum size of a module is governed by the maximum load that can be transported on the road. Often a building will be made up of multiple modules of varying sizes and shapes, which can be placed side-by-side or end-to-end, are able to be stacked, and can cantilever.
2. Modular buildings aren’t as robust as traditional builds
In some cases, modular buildings can be temporary and relocatable, however, this doesn’t mean they’re not well-built. Modular buildings that are installed for permanent use have been known to last as long as traditional buildings.
At Modscape, our modular homes can meet Cyclone Building codes at all levels, and we have installed several prefabricated house projects on the coast of north-western Australia (where our homes were easily able to meet these mandatory standards).
The steel frame we use provides the required structural integrity to meet Cyclone Building codes Australia-wide. Meanwhile, double-glazed windows, the option of external shutters and built-in inclusions further contribute to making Modscape an excellent choice for cyclone-affected areas.
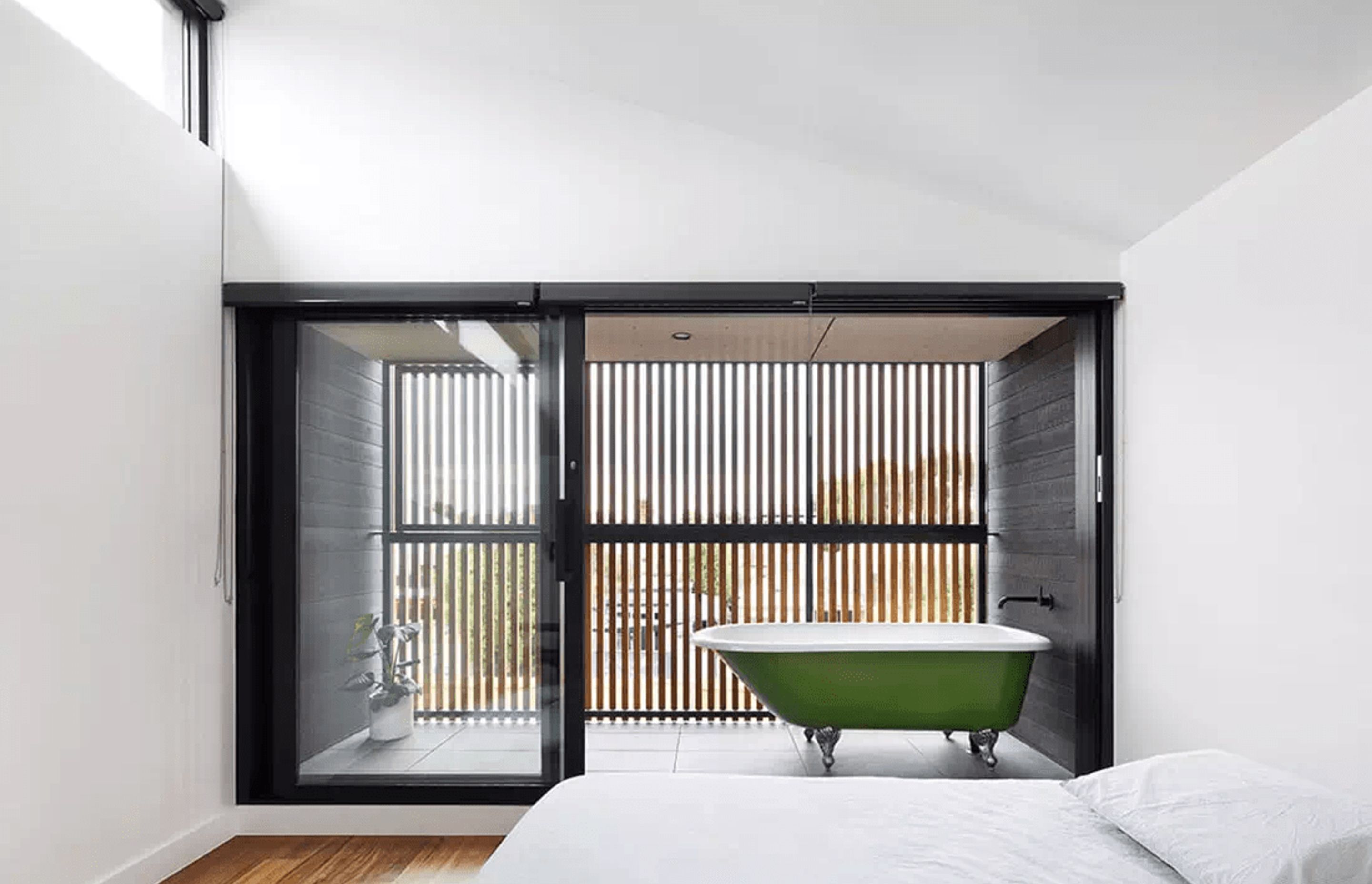
3. Prefabrication dulls the creative process for architectural design teams and clients
There’s a common misconception that modular buildings are just ‘boxes’ or ‘shipping containers’ stacked together, with no architectural aesthetic considerations. Unfortunately, this notion is one that has plagued the industry for years, but it is quickly being dispelled. All you need to do is look at contemporary modular designs – like ours – and you’ll soon realise that just about anything is possible!
There is plenty of diversity in design outcomes for both architects and clients. At Modscape, our steel frame modules can span large distances which give us great flexibility in the design and allows us to easily create large open spaces without the need for columns. Additionally, modules can be arranged in myriad ways to create any configuration of space, any shape and size. We can build angular or curved walls, pitched roofs and can even combine modules to create elliptical form.
On top of this, blocks of land that present geographical challenges for ordinary construction methods can be more easily catered to with modular design. For example, unusually steep blocks may be difficult to build on but can be accommodated by engaging modular construction, as all modules can be constructed in a factory without the challenges and hazards presented by building directly on the sloping land – thereby making the project achievable.
A testament to the design flexibility of modular construction is the growing popularity of prefabricated luxury homes. As reported by The Wall Street Journal, a $1.695 million (USD) modular vacation home has been built in Ventura, California, which features four bedrooms, four bathrooms, an open-concept floor plan, a chef’s kitchen, engineered hardwood floors and a master bedroom with a private patio and soaking tub. Similarly, a New York seven-bedroom, nine-bathroom modular home with a pool, pool house, decking, geothermal and solar-power systems and a green roof sold in 2020 for its full asking price of $4.695 million (USD).
Down Under, we’ve similarly taken clients’ dreams and made them a reality. Our marquee residential projects, such as Tamarama and Albert Park, showcase the possibilities of modular design, with many of our Homes in Progress set to add to our ever-growing portfolio of high-end home design and construction.
4. Modular builds are a rip-off!
In the case of Modscape, the cost of our bespoke modular homes is often compared against low- and mid-tier traditional builds, which can lead to some confusion. What many don’t realise is that all our homes are custom-designed by our in-house team of architects to meet each client’s individual requirements, site, and budget.
A modular process requires full design resolution and documentation before any works can be undertaken, which means we know exactly what we are building and exactly how much it will cost before we begin construction – so you won’t run into any unexpected nasties!
This enables us to deliver absolute price certainty and avoids you ever encountering what we call the ‘Grand Designs’ experience – architectural drawings coming in way over budget, price blowouts and timelines not adhered to, something those who have built traditionally experience more often than not. With us, the cost you are given at the contract stage is exactly what you will pay.
This process also means we can work backwards from your budget and create a design that we can guarantee will fit your constraints and budget perfectly.
There’s also the end-cost savings associated with a modular builder like Modscape. A faster build-time allows you to minimise holding costs of land or temporary accommodation costs, and the minimal on-site time reduces any travel/call-out fees. And, of course, there’s the money you’ll save on energy costs, as all our modular homes meet 6-Star energy rating requirements, with the possibility of achieving a higher rating depending on the design.
So, no – modular homes aren’t overpriced. In fact, we believe they’re exceptional bang for the buck, all things considered.